En 2014, Richards-Wilcox Conveyor instaló un sistema básico desmontado para Clyde Machines. Ahora, Clyde necesitaba un sistema mucho más eficiente y flexible para apoyar sus nuevas operaciones.
Richards-Wilcox Conveyor se puso creativo con el diseño para ampliar la capacidad de Clyde con un sistema de transporte personalizado para sus nuevas instalaciones. Tomamos los archivos del software de su arquitecto y los fusionamos con nuestros archivos de diseño para asegurarnos de que no hubiera columnas que obstruyeran el paso.
Trabajando estrechamente con Clyde durante el diseño del sistema, pudimos superar sus expectativas y reducir el espacio previsto.
Otro reto importante en el diseño de la línea de pintura de Clyde Machines fue la multitud de tamaños y pesos diferentes de las piezas que debían transportarse, algunas de hasta 2.500 libras. Esto sólo significa una cosa. Era el momento de construir un sistema más fuerte diseñado para la evolución.
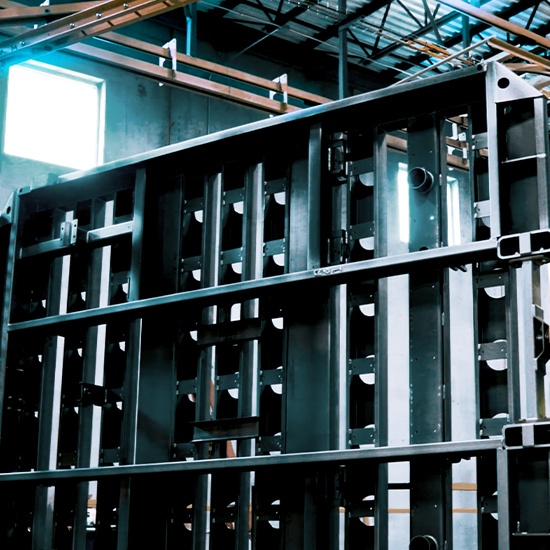

«Cuando conocimos a Dan, el representante de Richards-Wilcox de Divine Industrials Sales, hizo lo que hace cualquier buen vendedor, decir ‘Sí, podemos hacerlo’. Pero Richards-Wilcox realmente podía, y lo hicieron. No podíamos creer el resultado».
Todos a bordo del nuevo diseño.
Con esa actitud de poder hacer, trabajamos estrechamente con Clyde Machines para desarrollar un sistema de transporte inteligente y racionalizado. Ayudamos a Clyde a diseñar la estructura del techo para soportar el sistema de transporte. Esto redujo el coste del proyecto y eliminó la necesidad de soportes en el suelo que se convierten en obstáculos en el proceso. Este paso no suele estar previsto antes de la construcción del edificio.
A continuación, construimos un sistema de control central totalmente integrado y conectamos el sistema de control de cintas transportadoras de Richards-Wilcox con el sistema informático de Clyde. Esto permitió que las piezas únicas en la parada de carga fueran rastreadas con el equipo de acabado mientras viajaban por el sistema.
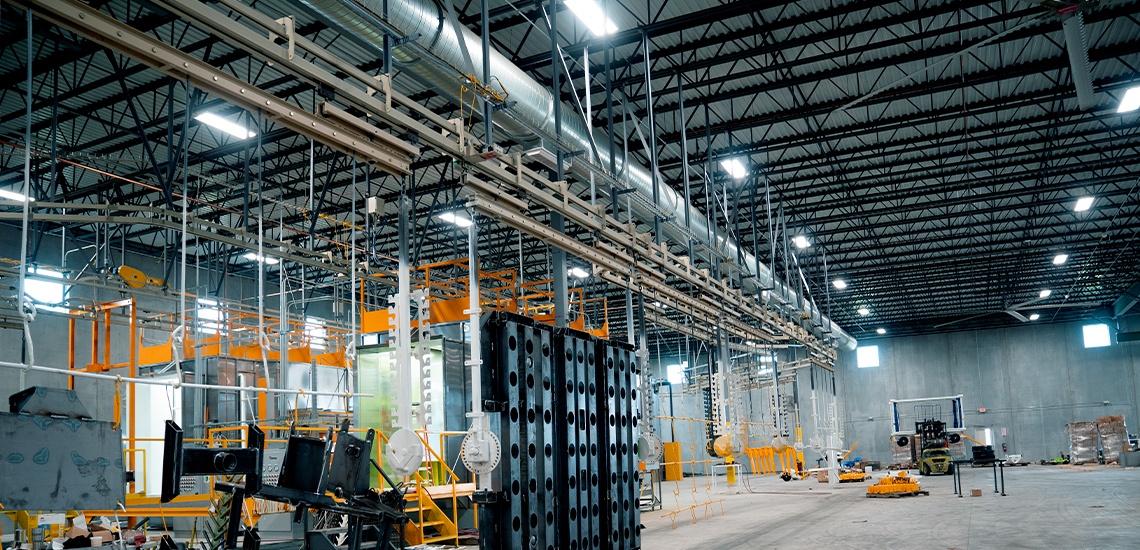
La interfaz optimizada escanea las piezas para determinar cuáles son, calcula la distancia exacta a la que deben colocarse para pintar y transmite la información al equipo de acabado.
Equilibrar la automatización con controles personalizables fue la clave para maximizar la productividad de Clyde.
El nuevo sistema integra una cabina de chorro de arena robotizada, una cabina de pintura automática de «velocidad lenta», una cabina de pintura manual y un horno de tiempo de curado ajustable; cada función personaliza el control para minimizar la mano de obra y maximizar el rendimiento.
«Estamos pintando 3 veces el producto en nuestro nuevo sistema, con la mitad de gente».
También hemos incorporado una alarma para las raras ocasiones en las que un error humano interrumpe el flujo, lo que hace que sea realmente fácil de reiniciar y volver a poner en marcha en cuestión de minutos.


¡Despejado para el despegue!
Finalmente, Richards-Wilcox Conveyor diseñó un sistema con potencial para pintar todo hasta 2500 libras, mejorar el margen de beneficios y hacer el proceso más eficiente en general. Con el nuevo transportador inteligente racionalizado, ayudamos a este líder en equipos de apoyo en tierra para aeronaves a entrar en la pista de la evolución.