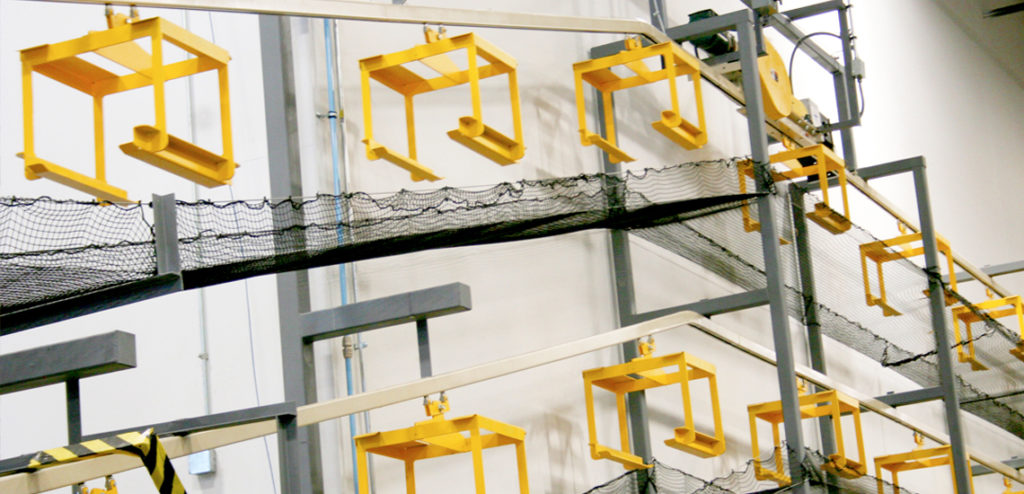
La operación de Dematic Corporation en Fort Worth es la mayor planta de fabricación de equipos de clasificación postal del mundo. Sus productos afectan a todos. Sólo el Servicio Postal de EE.UU. entrega más de 500 millones de piezas de correo cada día; cada vez que una carta llega a la dirección correcta, es porque, en algún momento, una máquina la clasificó. (Probablemente una máquina de Dematic Corporation).
Aunque las instalaciones de Fort Worth ya se encontraban entre las operaciones más productivas del mundo, carecían de eficiencia en varias áreas clave: costaban a Dematic Corporation tiempo, dinero y precisión. También puso en riesgo la salud de algunos de los trabajadores.
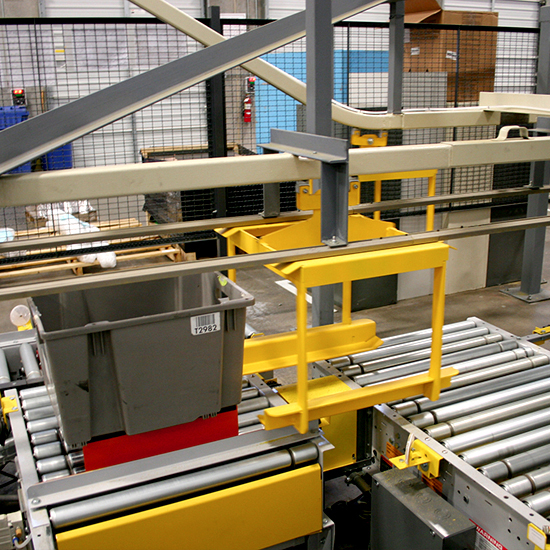
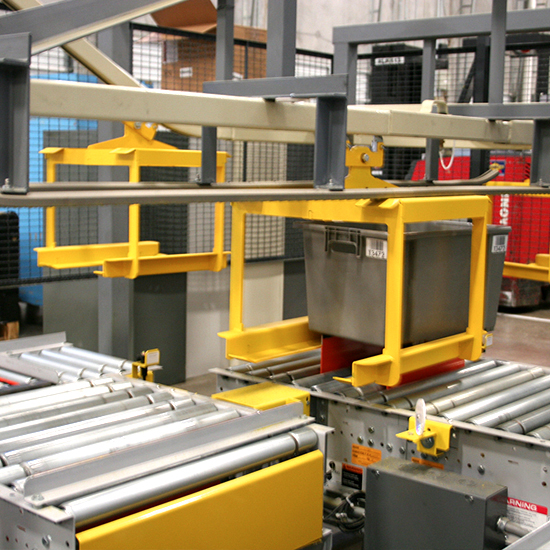
Este es el núcleo del problema: el funcionamiento del almacén de Dematic Corporation requería demasiada mano de obra. Demasiadas cosas eran manuales. Los trabajadores recibían y almacenaban las piezas a mano. La preparación de la producción se realizaba manualmente con un antiguo sistema de recogida de papel. Cuando llegaban los artículos, los empleados los cargaban en pesados contenedores, que pesaban hasta 80 libras, y los empujaban por el suelo de hormigón. Empujar estas pesadas cargas era malo para la salud de los trabajadores y también para los contenedores, que se desgastaban rápidamente.
En conjunto, estos elementos obsoletos eran desastrosos para la productividad. Con un sistema de manipulación de materiales tan ineficaz, la producción a menudo se quedaba sin piezas a la espera de la entrega de los kits. (Y los responsables de las instalaciones no odian nada más que las esperas).
Para maximizar la productividad en Fort Worth, Dematic Corporation tuvo que revolucionar sus métodos de recepción y envío de inventario. Se asociaron con Richards-Wilcox Conveyor para encontrar una respuesta.
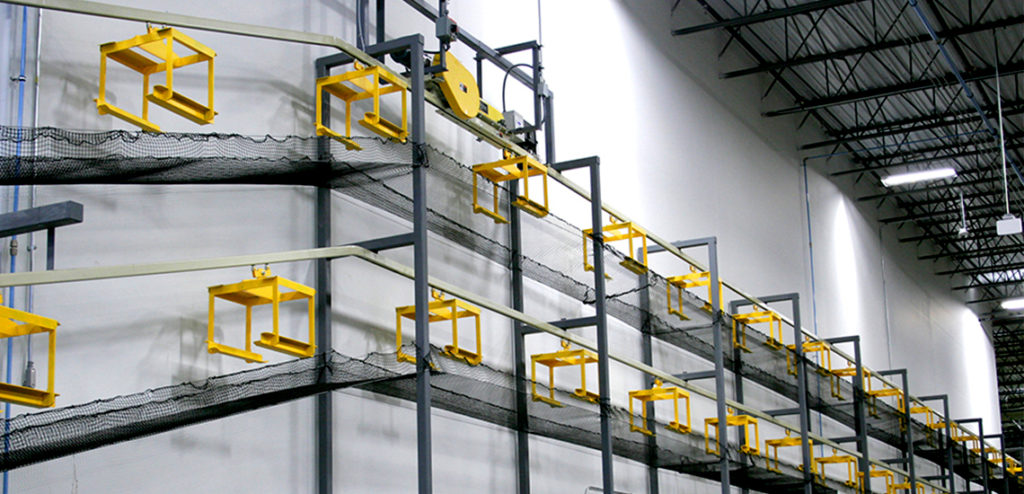
Nuestro equipo diseñó una solución totalmente personalizada que revisó su funcionamiento actual. Trabajamos con otros proveedores para analizar las instalaciones de Fort Worth y diseñar el nuevo sistema, que incluye carruseles horizontales, bahías de recogida, estanterías y un transportador de rodillos.
Hoy en día, un transportador aéreo Richards-Wilcox Zig-Zag® de 1.100 pies de largo es la columna vertebral de la operación de Fort Worth, conectando varios sistemas e integrando todos los demás equipos.
El transportador aéreo es ahora el principal dispositivo de entrega de todos los contenedores, eliminando la necesidad de que los trabajadores arrastren objetos pesados por el suelo. El sistema se integra perfectamente con el transportador de rodillos, poniendo en escena y depositando los contenedores en el carrusel horizontal y entregando los kits terminados a las estaciones de descarga en carriles desviados. Aprovechando el espacio aéreo no utilizado, el monorraíl Zig-Zag® realiza varios cambios de elevación para despejar los equipos y la maquinaria, mientras funciona a una velocidad constante de 45 FPM.
El nuevo sistema está ampliamente automatizado. Sin detener el funcionamiento del transportador aéreo, los contenedores se cargan automáticamente en el primer soporte vacío disponible en cuatro puntos de carga. A continuación, se descargan automáticamente en el destino adecuado en función de una identificación introducida por Dematic Corporation.
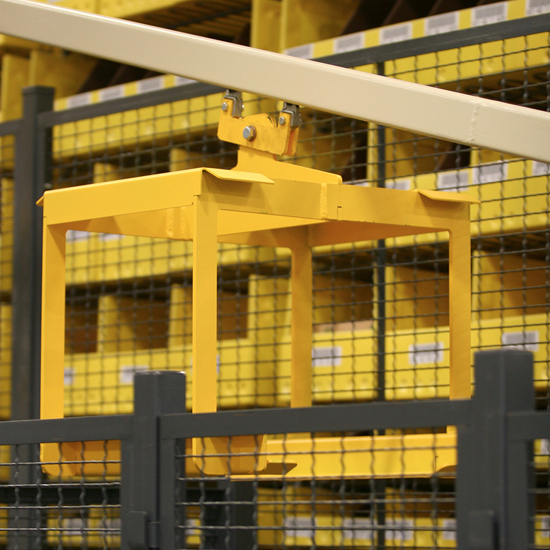
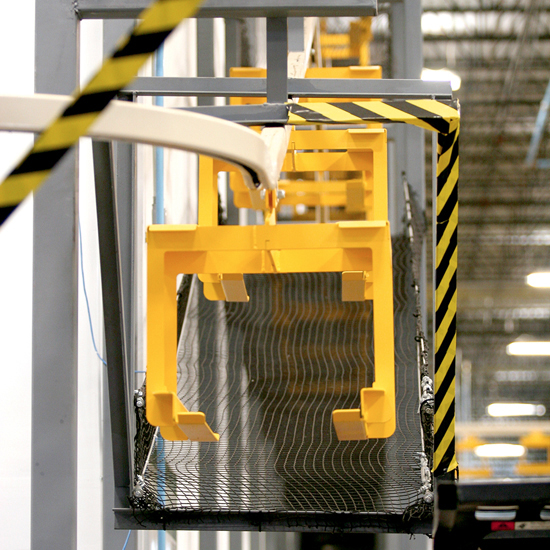
Las estaciones de descarga retiran automáticamente el contenedor del transportador aéreo en movimiento. Una vez que el contenedor está libre del portador en el área del carrusel, una transferencia lo llevará al transportador de rodillos de acumulación que conduce a la estación de trabajo. En el caso de los desvíos de kits, una sección corta de rodillos motorizados desplaza el contenedor activo a una sección de la cinta transportadora que se desplaza por gravedad. Allí se acumulan los totes. Las estaciones de recogida tienen una transferencia, colocando el contenedor delante de un portador vacío en el transportador aéreo. Un tope mantiene la bolsa en su sitio mientras el transportista la recoge sobre la marcha.
El contenedor completado se empuja hacia la cinta transportadora de recogida y se transporta a la estación de recogida de la cinta transportadora superior. Cuando llega el primer transportista vacío, la estación transfiere el contenedor para su recogida. A continuación, el contenedor se transfiere automáticamente al sistema de transportadores aéreos y se entrega a las zonas de preparación de kits, donde se trasladan para su transporte a las instalaciones de fabricación.
Aprovechando las tecnologías automatizadas y aprovechando al máximo el espacio antes no utilizado, el nuevo sistema de Fort Worth es radicalmente más eficiente, y Dematic Corporation está viendo los resultados.
En la actualidad, el centro ahorra unas 12.480 horas de trabajo al año y experimenta un aumento del 80% en la productividad.