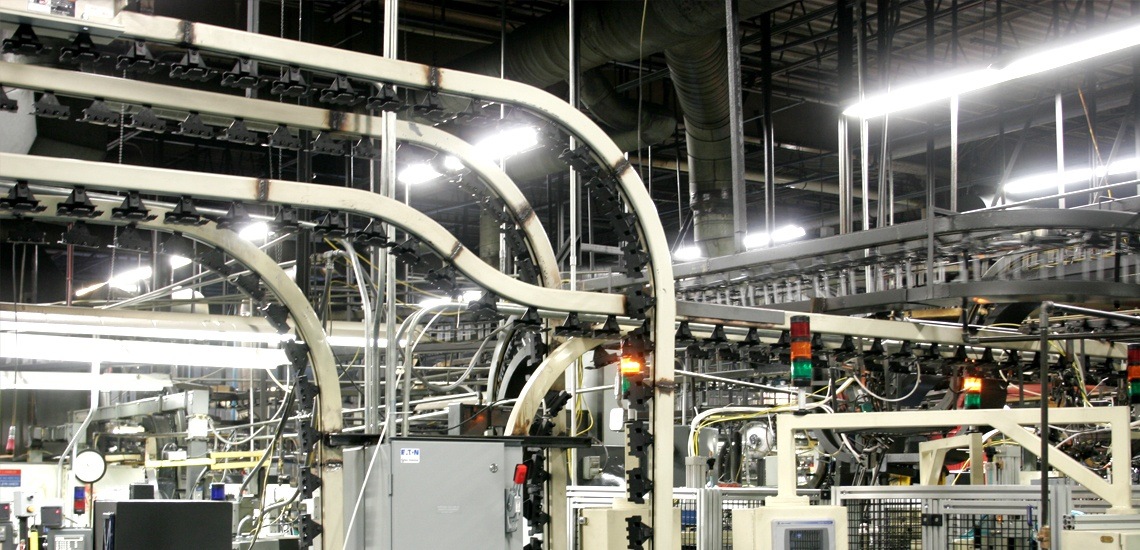
Las válvulas de motor de Eaton Corporation hacen que su coche funcione mejor, en casi todos los sentidos. Aumentan el ahorro de combustible, mejoran la eficiencia y aumentan el rendimiento general. Las válvulas, en otras palabras, son una maravilla de la ingeniería. Ahora, también lo es la instalación que los produce.
Casi todos los fabricantes de automóviles y motores del mundo utilizan válvulas de motor Eaton. (Probablemente haya uno en tu coche ahora mismo). La demanda no podría ser mucho mayor; Eaton produce más de un millón de válvulas de motor cada día. Con un volumen de producción tan elevado, la empresa siempre busca aumentar su eficiencia: más rápida, más ajustada, más precisa y lo más automatizada posible.
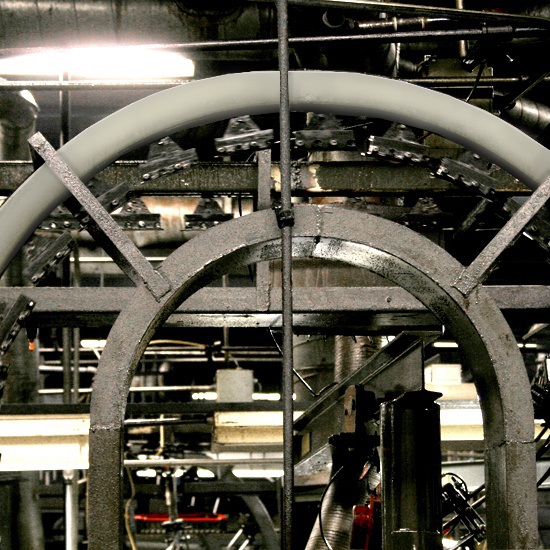
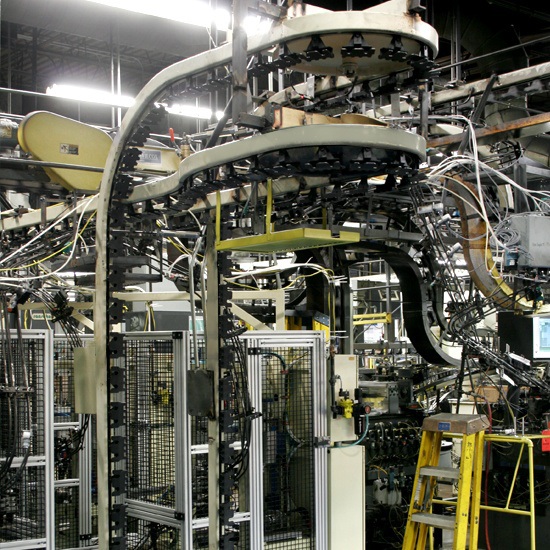
Cuando Eaton acudió a Richards-Wilcox, nos planteó un reto: Tomar nuestra planta de fabricación en Kearney, Nebraska, y transformarla en la fábrica de Eaton más eficiente del mundo.
Nos rompimos los nudillos y nos pusimos a trabajar.
En la actualidad, la columna vertebral de la operación de fabricación de Kearney es un transportador aéreo monorraíl Richards-Wilcox hiperpersonalizado. Con 12.000 pies de giros, vueltas, curvas, bucles y una compleja serie de procesos automatizados, es uno de los sistemas de transporte más elaborados e ingeniosos de la industria.
Aparte del mantenimiento anual, las instalaciones de Kearney nunca se detienen. Funciona las 24 horas del día. Cerca del principio de la línea, las válvulas se extruyen a partir de lingotes de acero, y los trabajadores los colocan en contenedores. Esa es la última vez que los productos son tocados por manos humanas, hasta que llega el momento de empaquetarlos y enviarlos.
El resto está totalmente automatizado. La cinta transportadora lleva las válvulas a través de una montaña rusa de procesos automatizados perfectamente integrados: lavado, esmerilado, lijado y otros procesos de fabricación de las válvulas. A lo largo de este tramo se realizan un total de 16 operaciones distintas, todas ellas automatizadas. La alta concentración de operaciones es casi inédita, y sólo es posible porque se ha encajado un gran número de curvas y bucles en un área extremadamente pequeña.
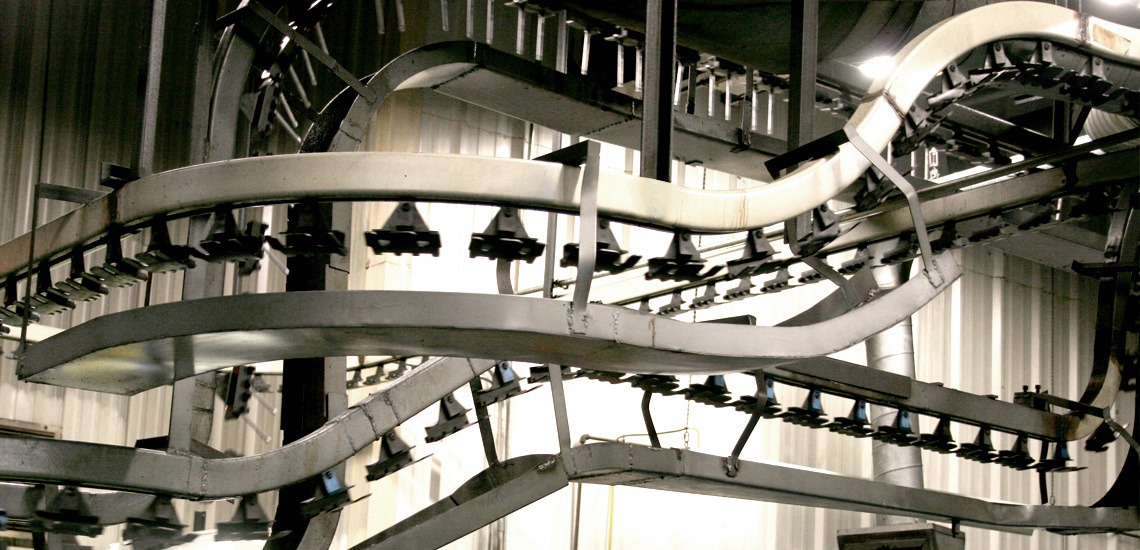
Joe Bash, director de las instalaciones de Eaton en Kearney, afirma que la calidad de la pista le ha permitido realizar fácilmente las complejas modificaciones para aprovechar al máximo su espacio. Al cortar el riel, Joe señala que el material no se «ensancha», a diferencia de los rieles laminados de menor calibre. Por lo tanto, una sola sección de vía de 3 metros puede cortarse varias veces, creando un desplazamiento para rodear la maquinaria. Joe puede incluso cortar una curva de vía de 9″ de radio sin ninguna dificultad.
«El producto de Richards-Wilcox es flexible y la calidad es excelente», dice Joe. «Ahora, no todo tiene que ser en línea recta».
¿El resultado? Con un sistema de transporte que lleva la eficiencia al máximo, las instalaciones de Eaton en Kearney se han transformado en una bestia de la fabricación con una productividad sin igual. El sistema anterior funcionaba manualmente, con trabajadores que cargaban las líneas de lotes. Ahora, con un sistema casi totalmente automatizado diseñado a lo largo de un transportador Richards-Wilcox, un solo operario atiende 6 máquinas. Los tiempos de cambio se han reducido radicalmente: de 8 horas a tan sólo 15 minutos. Gracias a las líneas divididas, la instalación puede gestionar tiradas menores con la máxima eficiencia, sin dejar de ofrecer la fabricación JIT.

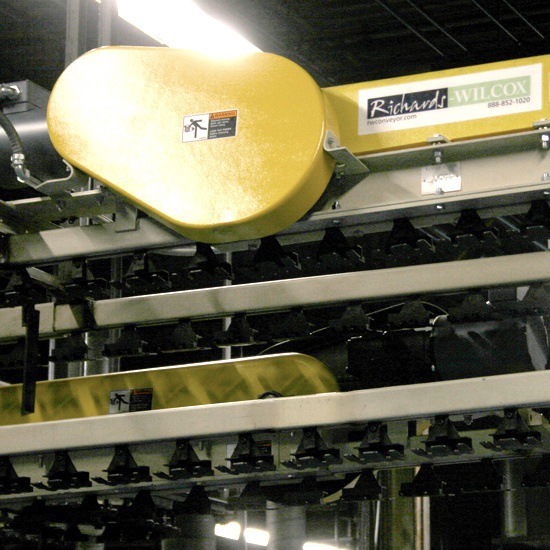
Joe dice que el nuevo transportador Richards-Wilcox ha abierto oportunidades sin precedentes para su fábrica.
«Si la dirección me hubiera pedido que creara este sistema hace 20 años, esto habría sido imposible. Estas ventajas en cuanto a costes me abrieron un mundo nuevo».