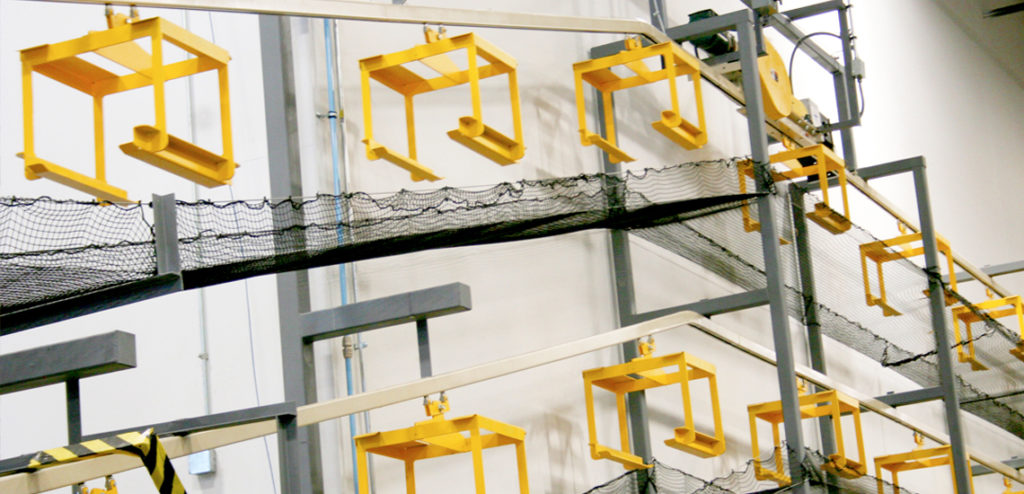
Dematic Corporation’s Fort Worth operation is the largest manufacturing plant of postal sorting equipment in the world. Their products affect everyone. The US Postal Service alone delivers more than 500 million pieces of mail each day; Any time a letter arrives at the correct address, it’s because, somewhere along the line, a machine sorted it. (Probably a Dematic Corporation machine.)
Although the Fort Worth facility was already among the world’s most productive operations, it lacked efficiency in several key areas: costing Dematic Corporation time, money and accuracy. It also put some of the workers’ health at risk.
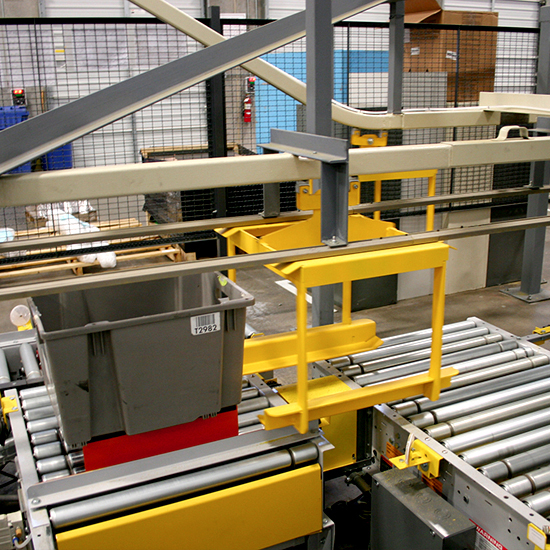
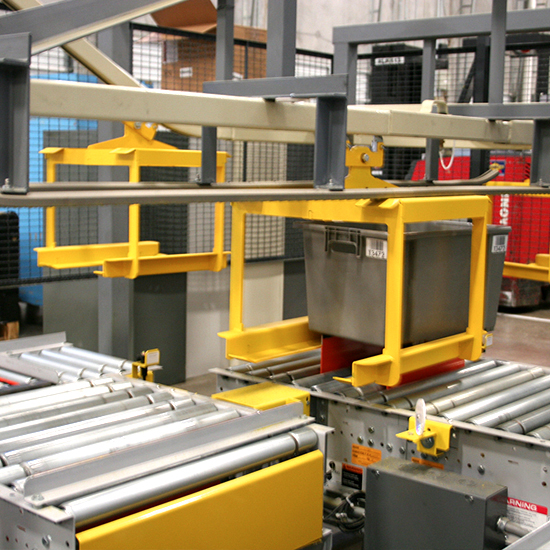
Here’s the core of the problem: The Dematic Corporation’s warehouse operation was overly labor-intensive. Too much of it was manual. Workers received and stocked parts by hand. Kitting for production was performed manually with an old paper pick system. When items arrived, employees loaded them into heavy totes, weighing as much as 80 pounds, which they pushed across the concrete floor. Pushing these heavy loads was bad for the workers’ health and bad for the totes, too, quickly wearing them down.
Together, these outdated elements were disastrous for productivity. With such an inefficient material handling system, production was often starved for parts as they waited for kits to be delivered. (And facility managers hate nothing more than waiting.)
To maximize productivity in Fort Worth, Dematic Corporation had to revolutionize their methods of receiving and shipping inventory. They partnered with Richards-Wilcox Conveyor to find an answer.
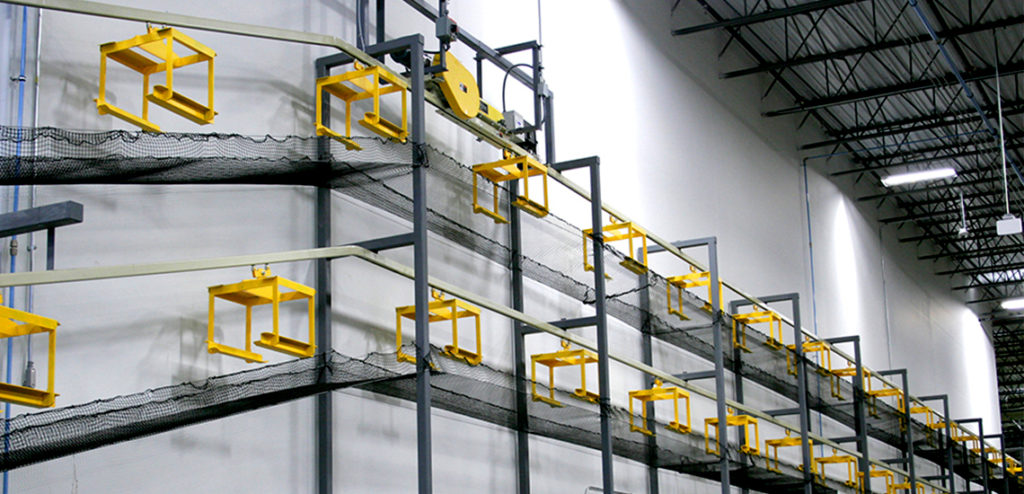
Our team engineered a fully customized solution that overhauled their current operation. We worked with other suppliers to analyze the Fort Worth facility and design the new system, which includes horizontal carousels, pick bays, racks and a roller conveyor.
Today, a 1,100-foot-long Richards-Wilcox Zig-Zag® Monorail overhead conveyor is the backbone of the Fort Worth operation, connecting various systems and integrating all other equipment.
The overhead conveyor is now the primary delivery device for all totes, eliminating the need for workers to drag heavy items across the floor. The system seamlessly integrates with the roller conveyor, staging and depositing totes at the horizontal carousel and delivering finished kits to unload stations in diverted lanes. Exploiting unused overhead space, the Zig-Zag® monorail makes several elevation changes to clear equipment and machinery, while running at a constant 45 FPM.
The new system is largely automated. Without stopping operation for the overhead conveyor, totes are loaded automatically onto the first available empty carrier at four load points. Then, they are automatically unloaded at the proper destination based on an ID entered by Dematic Corporation.
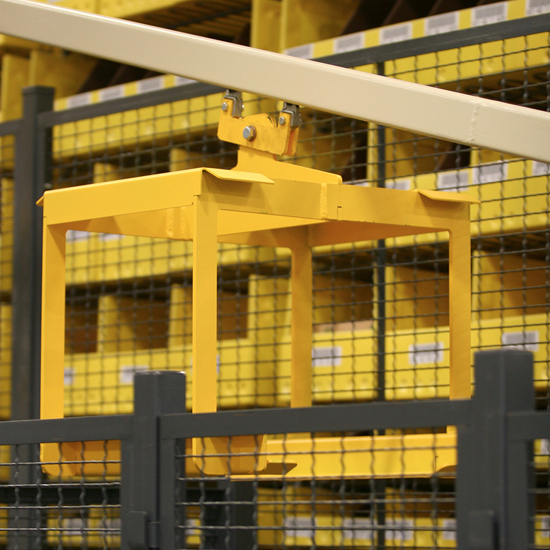
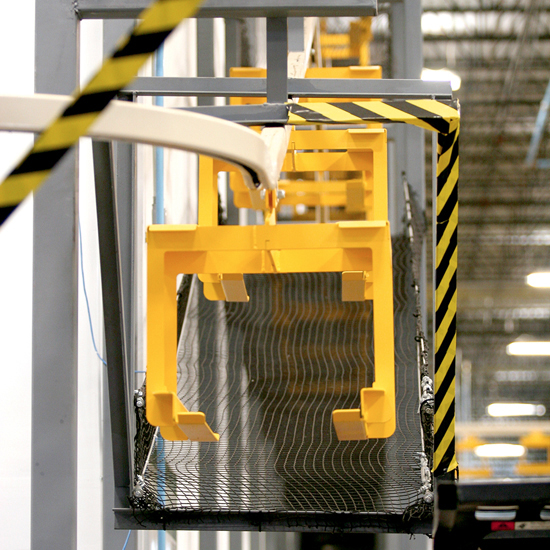
Unload stations automatically remove the tote from the moving overhead conveyor carrier. Once the tote is clear of the carrier in the carousel area, a transfer will move the tote to the accumulation roller conveyor leading to the work station. For the kitting diverts, a short section of powered roller moves the active tote onto a gravity-run out section of conveyor. There, the totes are accumulated. Pick-up stations have a transfer, placing the tote in front of an empty carrier on the overhead conveyor. A stop holds the tote in place as the carrier picks it up on the fly.
The completed tote is pushed onto the takeaway conveyor and transported to the overhead conveyor pick-up station. When the first empty carrier arrives, the station transfers the tote for pick-up. The tote is then automatically transferred to the overhead conveyor system and delivered to the kitting areas, where they are moved for transport to the manufacturing facility.
Leveraging automated technologies and making the most of previously unused space, the new Fort Worth system is radically more efficient, and Dematic Corporation is seeing the results.
Today, the facility is saving an estimated 12,480 labor hours annually and seeing an 80% increase in productivity.