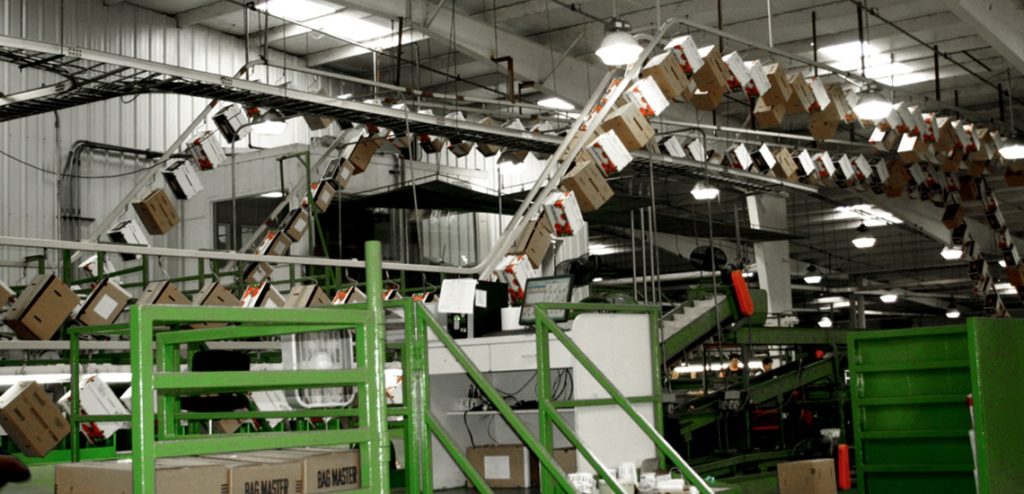
The modern conveyor system offers an efficient and cost-effective way to distribute goods in a variety of industries. Whether it be moving materials, packages, or parts, the right conveyor system helps you streamline production and minimize losses.
Yet as beneficial as conveyors are to productivity, there are some common challenges associated with them that can cause downtime and impact overall efficiency.
Let’s take a look at the most common issues customers experience with conveyors and explore some dynamic solutions that can increase operating profits while decreasing waste. As well as the benefits that come with implementing evidence-based solutions through Richards-Wilcox Conveyor – one of the leading industrial automation companies in North America.
The Top Conveyor Distribution Challenges and How to Solve Them
Conveyors are a vital part of the distribution system in many industries, but they can come with their own set of challenges.
1. Know Everything About What You’re Moving
In order to optimize the conveyor system, you need to know everything about what you’re moving. This includes the weight, size, shape, and fragility of the items you’re moving, as well as environmental factors such as temperature, humidity, and dust. Without properly accounting for all of these factors, your system may not be able to function correctly and could lead to costly repair and maintenance bills.
The Solution: To ensure the proper functioning of your conveyor system, you must take the time to understand the exact parameters of the items you’re moving. With Richards-Wilcox Conveyor’s advanced conveyor engineering, you can receive a custom-made conveyor solution tailored to the exact needs of your business.
2. Improper Maintenance or Lack of Maintenance
Proper maintenance is essential to keep any conveyor system running at peak performance. Unfortunately, many businesses fail to dedicate enough time and money to maintain these systems. This can lead to an inefficient system, as well as costly repairs and maintenance bills.
The Solution: Richards-Wilcox Conveyor’s maintenance programs are designed to help you get the most out of your conveyor system. Our team of experts can help you design and implement a maintenance program tailored to the specific needs of your business. This will help keep your system running smoothly and reduce downtime.
3. Inadequate Design
The design of your conveyor system is critical to its success. If the system is not designed properly, it can lead to costly repairs, inefficient operation, and prolonged downtime. These issues can have a major impact on your bottom line.
The Solution: The team of experienced engineers at Richards-Wilcox Conveyor can help you design the perfect conveyor system for your business. We will work with you to understand your specific needs and develop a system that is both cost-effective and efficient.
4. Dirty and/or Hazardous Locations
Contaminants and hazardous materials can wreak havoc on conveyor systems. These materials can cause corrosion, blockages, or even fires. This can lead to costly repairs and downtime, not to mention, they can be a danger to both you and your employees.
The Solution: An optimized industrial conveyor system from Richards-Wilcox Conveyor can help you avoid these dangerous and costly problems. Our systems are designed with the utmost safety and reliability in mind, and our team of engineers can help you customize a solution that meets your specific needs, even in the most challenging environments.
5. Poor Distribution Efficiency
An inefficient distribution system can lead to lost profits and damage your bottom line. If your system is not working correctly, it can cause slowdowns in production and delays in shipping and delivery. Inadequate inventory management can also lead to additional costs as you are paying for stock that isn’t moving.
The Solution: With Richards-Wilcox Conveyor’s automatic inventory management system, you can eliminate these problems and improve the efficiency of your distribution system. Our advanced technology can help you label, track, and trace all products, ensuring that the right items are shipped on time and minimizing the amount of stock you are carrying.
6. Timely Manual Processes
Manual processes can be time-consuming and require an operator to be constantly on hand. Automation is a great way to reduce manual processes. Automated systems can be set up to operate without a person present, and even identify areas of inefficiency and issue reports. When combined with advanced real time analytics, this can create a powerful, cost-effective solution for better tracking and accountability.
The Solution: Utilizing data-driven analytics and technology to identify areas of inefficiencies in manual processes can help reduce time and costs in the distribution system. An automated system can streamline the process and accurately monitor performance over time. Richards-Wilcox Conveyor offers a wide range of automated solutions and real-time analytics to make distribution more efficient and cost effective.
7. Lack of Visibility in Your Inventory
Maintaining accurate inventory tracking can be a real challenge. If inventory numbers are inaccurate or outdated, it can lead to unforeseen delays and costly mistakes. A lack of visibility also makes it difficult to identify damaged or missing items and effectively track inventory performances.
The Solution: Utilizing RFID technology can help increase visibility and accuracy in tracking inventory. RFID tags can be placed on each item, enabling real-time scanning and tracking. This data can be linked to analytics software for better visibility and tracking of inventory.
8. Lower Transport Efficiency
Lower transport efficiency can lead to longer delivery times, higher operational costs, and customer dissatisfaction due to inaccurate tracking. Having an efficient and cost-effective transport system is essential to any business, especially in the delivery of goods.
The Solution: Utilizing a conveyor-based system can significantly improve transport efficiency. With a wide range of options, Richards-Wilcox Conveyor can create an efficient, automated transport system that moves items through the distribution system quickly and accurately. This can help reduce operational costs and increase customer satisfaction.
Fortunately, there are several solutions that can help businesses address these problems. Dynamic solutions such as improved alignment techniques, upgraded support structures and updated components help ensure smooth operation while comprehensive training and preventive maintenance programs allow for better management of resources and increased productivity.
Implementing evidence-based initiatives like those offered by Richards-Wilcox Conveyor is also key; their advanced systems offer superior control over all aspects of conveyor operations including speed regulation, pressure monitoring and load balancing – ensuring optimal performance every time.
The Benefits of Implementing Dynamic, Evidence Based Conveyor Solutions
Dynamic, evidence-based conveyor solutions offer a range of benefits for businesses in any industry.
By streamlining production and minimizing losses through improved alignment techniques, upgraded support structures and updated components, conveyors can increase efficiency while decreasing downtime.
Through comprehensive training and preventive maintenance programs that address common issues like misaligned belts or worn-out parts, businesses can better manage resources and increase productivity.
Moreover, implementing advanced systems such as those offered by Richards-Wilcox Conveyor ensure superior control over all aspects of operations including speed regulation, pressure monitoring and load balancing – ultimately leading to faster completion times with fewer errors. By investing in dynamic solutions that are based on the latest research and technology trends available today, companies can enjoy greater cost savings while gaining an edge over their competitors when it comes to efficient distribution processes.
The Importance of Conveyor Solutions for Industries
Conveyor solutions have become increasingly important for industries across the globe to help them maximize profits and reduce costs. In today’s competitive market, every business needs to be able to move products quickly and efficiently. By implementing a conveyor system, businesses can quickly transport goods from one place to another without the need for additional labor or costly equipment.
Furthermore, these solutions can help businesses reduce waste and improve safety conditions. By using efficient systems that are tailored to each business’s needs, companies can better manage their inventories and reduce human error. Additionally, with advanced technology like RFID tagging, companies can quickly track goods and ensure that shipments are delivered on-time.
Finally, conveyor solutions can also help businesses meet consumer demands faster. By cutting down on manual operations and improving production accuracy, companies can better respond to customer demands and generate more revenue. Ultimately, implementing dynamic conveyor solutions are essential for modern businesses looking to stay ahead of their competitors.
Benefits of Investing in Dynamic Conveyor Solutions
Investing in dynamic conveyor solutions can benefit businesses in numerous ways. First and foremost, it can help them reduce costs and increase efficiency. Automated conveyors can be tailored to meet the specific production, packaging and distribution needs of a company, saving time, money and labor.
In addition, investing in dynamic conveyor solutions can help businesses improve safety conditions and reduce accidents. Through advanced sensors, automated shutoffs and emergency stop systems, companies can ensure that their operations are more secure and controlled.
Finally, by investing in dynamic solutions, companies can significantly reduce their environmental impact. By investing in low-energy conveyors and reducing the amount of paper and plastic used for packaging, businesses can reduce their carbon footprint while still meeting the demands of their customers.
Ultimately, the benefits of dynamic conveyor solutions are vast and varied, making them an ideal investment for businesses of any size or industry.
How Richards-Wilcox Conveyor Can Help You Increase Operating Profits
Richards-Wilcox Conveyor is a leading industrial automation company that can help you increase operating profits through their advanced systems. By investing in evidence-based solutions, businesses can enjoy greater cost savings while gaining an edge over their competitors when it comes to efficient distribution processes.
Modern shipping requires dynamic solutions designed to streamline production and minimize losses by improving alignment techniques, upgrading support structures and replacing worn-out or broken parts.
With advanced systems that offer superior control over all aspects of conveyor operations including speed regulation, pressure monitoring and load balancing, you get optimal performance every time.
With these modernized solutions, companies can save money on labor costs while maximizing profitability with fewer errors. In addition to increasing efficiency throughout the entire transportation process, Richards-Wilcox Conveyor also offers analytics capabilities which allow customers to gain valuable insights into operational data for further optimization opportunities.
Ultimately this allows businesses to make more informed decisions about how they run their operations – resulting in higher profits at lower costs!