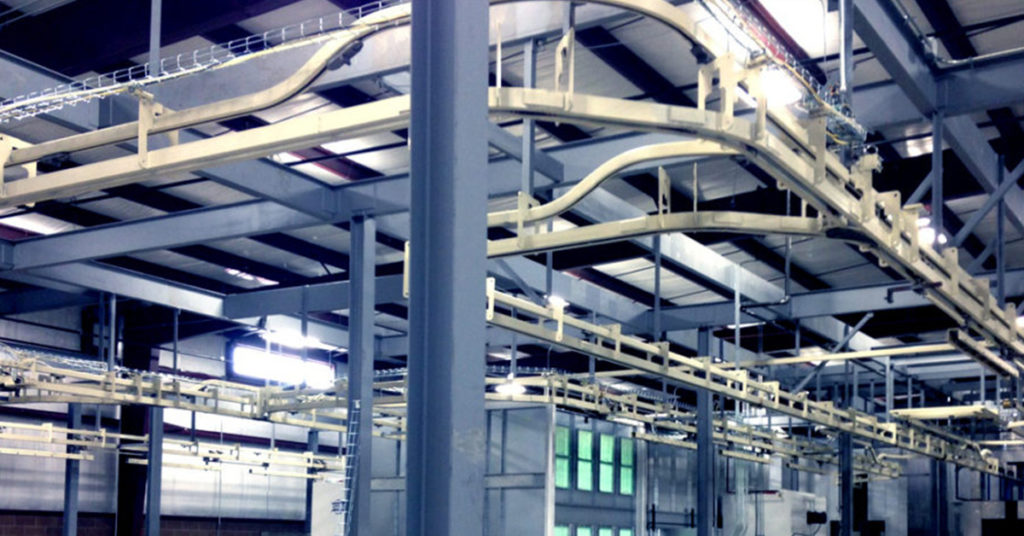
In manufacturing, efficient material handling is the backbone of productivity and profitability. Companies can streamline workflows, minimize waste, and maximize output by optimizing the movement, storage, and control of materials throughout production.
One innovative solution revolutionizing material handling is the heavy duty over-and-under conveyor. These advanced systems are designed to handle high volumes of materials with speed, precision, and flexibility, making them the ultimate choice for modern manufacturing environments.
Over-and-under conveyors offer a compact and efficient alternative to traditional material handling methods by transporting materials vertically and horizontally – utilizing multiple levels, optimizing space and reducing the footprint required for operations. Embracing this technology can significantly boost your manufacturing capabilities and keep you competitive in a rapidly evolving market.
What Are Over-and-Under Conveyors?
These conveyors facilitate both vertical and horizontal movement of materials, allowing for seamless transitions between different production stages.
Essential components include robust tracks, carriers that hold and transport materials, and advanced drive systems that ensure smooth operation. The Richards-Wilcox OveR-Way™ heavy duty over-and-under conveyor is particularly effective in handling large, heavy loads, making it a popular choice for industries like automotive and aerospace. These systems are part of custom material handling solutions that can be tailored to meet specific operational needs, providing flexibility and efficiency in material movement.
Advantages of Heavy Duty Over-and-Under Configurations
Heavy duty over-and-under conveyor systems offer a range of advantages that make them a standout choice for modern manufacturing.
1. Space Optimization and Increased Capacity
Over-and-under conveyors maximize vertical space utilization, allowing manufacturers to store and process materials at higher levels. This vertical movement increases overall capacity, enabling facilities to handle larger volumes without expanding their footprint.
Compared to traditional conveyors, which require extensive horizontal space, the OveR-Way™ heavy duty over and under conveyor minimizes the floor area needed for material transport. This efficiency is crucial for businesses with limited space as it allows for more effective use of their facilities.
2. Enhanced Throughput and Efficiency
These conveyor systems excel at simultaneous material handling, transporting multiple items at once. This capability significantly boosts overall throughput and ensures production lines run smoothly and efficiently.
The design of over-and-under conveyors also reduces the time it takes to move materials from point A to point B, leading to shorter cycle times. Faster material movement enhances productivity and helps manufacturers meet tight deadlines. This alone makes these systems invaluable for effective automated material handling.
3. Flexibility and Scalability
Adaptability is a key feature of over-and-under conveyors. These conveyors adapt easily to layout changes. As production needs evolve, manufacturers can reconfigure these systems without extensive downtime or costly renovations.
This adaptability allows businesses to scale operations efficiently, accommodating growth or shifts in product lines without significant infrastructure changes. Companies can respond quickly to the ebb and flow of market demands, ensuring they remain competitive.
4. Cost-Effectiveness and Improved Safety
Heavy duty over-and-under conveyors lower operational costs by reducing the need for manual handling. This automation minimizes labor expenses and decreases equipment wear and tear, leading to lower maintenance costs. The durability of these systems ensures a strong return on investment over time, as they require less frequent replacement or repair.
Additionally, these conveyors enhance workplace safety by minimizing the risks associated with manual material handling, reducing accidents and injuries. Investing in material handling and fabrication solutions like these not only streamlines operations but also creates a safer, more efficient work environment.
Key Applications of Heavy Duty Over-and-Under Conveyors
Over-and-under conveyors are essential in various manufacturing applications, providing efficient material handling solutions that enhance productivity and streamline operations.
Automotive Manufacturing
In automotive manufacturing, heavy duty over-and-under configurations are widely used to transport components between assembly stations. These conveyors facilitate the movement of heavy parts while minimizing the need for manual handling. Their design allows for efficient use of vertical space, enabling manufacturers to optimize their production lines and maintain a steady workflow.
Warehousing and Distribution
In warehousing and distribution centers, over-and-under conveyors improve the efficiency of sorting and transporting goods. They allow for simultaneous handling of multiple items, significantly increasing throughput. This capability is crucial for meeting the demands of e-commerce and rapid order fulfillment, where speed and accuracy are paramount.
Packaging Operations
Over-and-under conveyors are also utilized in packaging operations, where they transport products through various stages, including filling, sealing, and labeling. Their automated nature reduces labor costs and minimizes errors, ensuring a consistent and efficient packaging process. This aligns with the principles of automated material handling, allowing for seamless integration into existing systems.
Material Handling for Heavy Loads
These conveyors excel in environments that require the movement of heavy or bulky items, such as steel racks in manufacturing plants. They streamline material handling operations, reducing forklift and operator idle time. Investing in these systems enhances overall efficiency and productivity while optimizing material handling equipment.
Choosing the Right Heavy Duty Over-and-Under Conveyor System
Selecting the right heavy duty over-and-under conveyor system is crucial for optimizing your manufacturing operations. Here are key factors to consider.
Load Capacity
First, assess the load capacity your conveyor needs to handle. Heavy duty systems are designed for substantial weights, often exceeding 1,000 pounds per carrier. Ensure the conveyor you choose can accommodate your heaviest materials without risk of damage or failure.
System Layout
Next, consider your facility’s layout. Over-and-under conveyors excel in maximizing vertical space, making them ideal for facilities with limited floor area. Evaluate the available height and horizontal space to determine the best configuration for your operations.
Integration with Existing Systems
Companies should look for a conveyor that integrates seamlessly with their current material handling equipment. This ensures compatibility with existing systems, such as automated sorting or warehouse management software, to maintain a smooth workflow.
Customization Options
Customization options are essential for tailoring the conveyor to the company’s specific needs. Many manufacturers offer features such as adjustable speeds, specialized coatings, and varying lengths to fit unique operational requirements. This flexibility ensures that the conveyor system aligns perfectly with the production processes.
Industry 4.0 Integration
Prioritize models that offer seamless integration with Industry 4.0 technologies. Look for systems equipped with sensors and communication capabilities that enable real-time data collection, predictive maintenance, and enhanced connectivity with other manufacturing systems.
Safety Features
Finally, prioritize safety features. Choose conveyors equipped with safety interlocks and emergency stop functions. These features protect workers and minimize the risk of accidents during operation. Investing in a system that emphasizes safety not only protects the team but also the organization overall.
OveR-Way™ Heavy Duty Over and Under Conveyor
At Richards-Wilcox Conveyor, we understand the unique challenges manufacturers face in optimizing material handling. That’s why we’ve developed the OveR-Way™ Heavy Duty Over and Under Conveyor, a state-of-the-art system designed to streamline operations and boost productivity.
This innovative conveyor features a robust, heavy duty over-and-under configuration capable of handling loads up to 2,000 pounds per carrier. Its innovative design allows for both vertical and horizontal movement, maximizing space utilization and minimizing the footprint required for material transport. This efficiency is crucial for facilities with limited space, enabling them to optimize their layout and enhance workflow.
Customization is key, and we offer a range of options to tailor the OveR-Way™ conveyor to your specific needs. From adjustable speeds to specialized coatings, our team works closely with you to ensure the system aligns perfectly with your production processes.
Experience the power of the OveR-Way™ Heavy Duty Over and Under Conveyor and take your manufacturing operations to new heights. Contact us today to learn more about how this innovative solution can transform your facility.